Rhinoceros 5 4 2 – Versatile 3d Modeler Tutorial
Rhino 3D Software; Rhino 3D Modeling. The world's most creative people use the world's most versatile 3D modeler. Quickly develop designs and communicate with clients, colleagues, and collaborators. Learn More About Rhino Rhino for Windows. User Created Tutorial: Introduction to Smoothing Groups, Part 2: Smoothing Groups for a Car Model Introduction to Smoothing Groups, Part 2 Project: Smoothing Groups for a Car Model from Elvis “Lewis” Blazencic Thu 10 Jan 2019. Rhino Training and Tutorials. Build a 3D model using our Rhino 3D tutorials. Learn about 3D texture, industrial design, and rapid prototyping. Let our expert instructors take you on a tour of this popular 3D software. Start My Free Month. This 3D modeling software tutorial is written and designed to provide 3D printing enthusiasts with accurate instructions for designing 3D files that are 3D Printable thanks to Rhino 3D CAD software. In this 3D CAD tutorial, you will learn the best practices for modeling, correcting and exporting an object for 3D printing using Rhino software.
- Rhinoceros 5 4 2 – Versatile 3d Modeler Tutorials
- Rhinoceros 3d Mechanical Animation
- Rhinoceros 5 4 2 – Versatile 3d Modeler Tutorial For Beginners
Free 3D Design Webinar: Creating 3D Patterns with Grasshopper
This Wednesday we will present a new 3D design webinar in collaboration with Novedge, covering different design strategies forthe creation of 3D patterns and textures using Rhino and Grasshopper.
Introduction to Grasshopper for Designers (Free Webinar Recording)
The complete recording of our first exclusive webinar that gives an introduction to Grasshopper for Rhino, with an overview and a demonstration of the software specifically targeted to designers.
Engine Cover 3D modeling tutorial – Part 2
The second part of a 3D modeling tutorial that shows the creation of a styling model for an engine cover in Rhino3D. This video shows how to add detail and how to prepare the model for exporting into SolidWorks. Check Part 1 here.
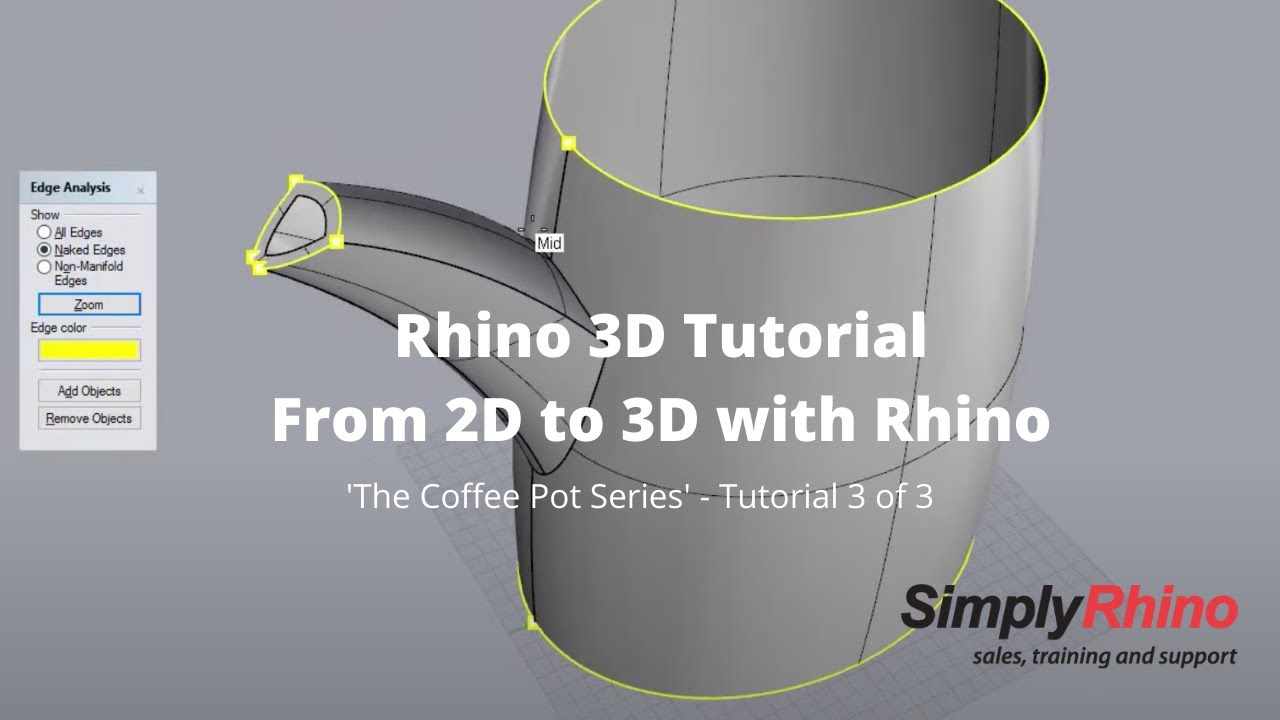
Engine Cover 3D modeling tutorial – Part 1
In this first part of video tutorials, senior instructor Phil Cook explains how to set up the main construction curves and basic slab surfaces and a number of tested strategies for making the corner blends.
Modeling Sunglasses in Rhino for Mac
A webinar presented by Kyle Houchens, who explains how to design sun glasses in Rhino 5 for Mac, using a real-world approach and creating a solid 3D model which is ready for 3-D printing or rendering.
Sketch to 3D Model – Detailing your model in Rhinoceros
A 50 minute webinar that shows the design workflow process for turning a 2D drawing into a detailed 3D model, taking as example a car wheel concept design.
Rhino and Solidworks Workflows
In this video designer Thomas Parel explains the main differences between using Rhino and SolidWorks and shows some techniques for integrating them together.
Modeling a car light in Rhino
This 44-minute video shows the 3D modeling process of a car stop light, done in Rhinoceros. A 3dm file is available for download.
Modeling Complex Transitions in Rhino
In this tutorial Brian James from McNeel explains how to model smooth transitions in Rhinoceros 5.0 using combinations of fillets, sweeps and network surfaces.
Modeling an Automotive Tire in Rhino V5
In this tutorial, Brian Oltrogge shows how to model a tire in Rhino version 5 using FlowAlongSurface and FlowAlongCurve.
Modeling an Automotive Rim in Rhino V5
In this video tutorial Brian Oltrogge from Grünblau Design Studio shows how to create a high quality 3D model of an automotive wheel rim using several advanced modeling techniques.
Easy Shut Lines in Rhino
A video tutorial by Scott Schneider, who explains how to use Rhino 5 new ApplyShutLining tool to create and evaluate panel parting lines in a non destructive way.
Advanced Filleting in Rhino
A collection of tutorials that show how to manually create fillets in situations where the automatic filleting tools in Rhino may fail.
3-D Printing Rhino Models
A 1 hour 20 minute long webinar presented by Kyle Houchens, who shows how to prepare a Rhino model for 3-D printing.
Rhinoceros 5 4 2 – Versatile 3d Modeler Tutorials
Class A Surfaces Part 2
In this second episode Michael Günther-Geffers from VSR explains the main criteria and requirements for Class A Surfaces and gives a workflow demo of the VSR plug-in tools in Rhino.
Class A Surfaces Part 1
The first part of a video tutorial on Class A Surfaces, explaining the meaning of the term and how surface transitions affect reflections. General overview applied to Rhinoceros and VSR Shape Modeling Plug-in.
3D Modeling Ear Buds in Rhino
In this 40 minutes video tutorial concept designer and instructor Kyle Houchens shows how to create a product 3D model starting from a reference sketch.
Freeform Modeling in Rhino
In this one-hour webinar James Carruthers of Hydraulic Design shows his basic modeling workflow, as well as a few advanced tricks for modeling complex freeform shapes in Rhino.
3D Printing With Rhino: Preparing Your Rhinoceros 3D Model for 3D Printing
Rhinoceros, or short Rhino, is a powerful and versatile modeling software for creating 3D designs. When you’re looking to 3D print your Rhino model, some points are very important to keep in mind: it needs to be watertight, exported correctly, and have the right wall thicknesses. While this might sound complicated, Kyle Houchens, an expert at preparing a Rhino 3D model for 3D printing, will show you how it’s done. In this step-by-step video tutorial, he will show you what kind of models are perfect for 3D printing and how you can identify and fix common mistakes.
Kyle has years of experience in 3D modeling and will be your instructor in this video series. He is also the owner of ‘The Outside’, a digital design consultancy specialized in 3D modeling, photo-realistic rendering, and finding solutions to any design problem.
So let’s prep our Rhino3D model for 3D printing!
1: Checking if your 3D Model is Watertight in Rhino
Kyle introduces the concept of a watertight model. Sometimes it’s also called a manifold model. Creating a watertight model literally means that no water could flow out of the model if it was being filled up. Kyle compares a watertight model to a water balloon. If you fill up a water balloon with water and tie the top of it and no water comes out, then that’s watertight. For 3D printing, creating a watertight model is a very important step.
The best way to find out whether your 3D model is watertight or not is with the ‘select open poly-surfaces’, ‘select bad objects’, and ‘edge analysis’ tools. In this first video clip, Kyle explains why these tools are so essential for creating a 3D printable model.
2: Creating a Polygon Mesh with the Right Tolerance in Rhino
In Rhino, you create an NURBS model, however, 3D printers print Polygon meshes. NURBS is a mathematical model whereas Polygon meshes are a collection of vertices, edges, and faces that define the model.
Critical to controlling the quality of your 3D printable model is how the model is meshed. Kyle will talk about how to control the mesh output in Rhino to an STL file and how to set units and tolerances in order to ensure a high-quality 3D print.
There is more than one way to control the mesh settings. In the following video, Kyle covers some of the other mesh settings, including the ‘Check’ tool, which may be useful as you convert your models to a mesh for printing.
3: Advanced Mesh Repair: Fixing Non-Watertight 3D Models in Rhino
In the first video, we learned how to see if your 3D model is watertight or not. Now, Kyle has created a non-watertight model and shows you which strategies you can use to fix the model and make it watertight.
You’ll notice that there are multiple ways of making your object printable in the following video clip.
4: Setting Wall Thickness and Hollowing a 3D Model in Rhino
Not all models are supposed to be 3D printed solid. Instead, they might be hollow inside and have walls with a certain thickness. Setting a wall thickness is important for 3D printing – if surfaces are paper-thin a printer wouldn’t have any information about how thick or how thin the surface is supposed to be.
That’s why Kyle will show you how to create hollow 3D models with a certain wall thickness.
Should you create a hollow model or not? Kyle says that it depends mainly on the size of your model. A model of his car that is just a few centimeters or inches long will work perfectly fine as a solid model. However, if this model was a bigger size, printing it solid would increase 3D printing costs significantly and (depending on the material) might even risk deformation of the print.
As a 3D print gets larger, you may want to hollow out the part to use less material. Kyle shows his methods of creating hollow parts in this last video.
Rhinoceros 3d Mechanical Animation
5: 3D Printing Your Rhino Model
Rhinoceros 5 4 2 – Versatile 3d Modeler Tutorial For Beginners
Now that your mesh is ready to go to the printer, you can upload it to our website, choose a 3D printing material, and let us take care of printing it for you.
Before you order your print, make sure to make yourself familiar with the 3D printing material of your choice. Each and every material is different and requires different minimum wall thicknesses, minimal detail sizes, etc. We put together a selection of design guides for the most popular 3D printing materials that will help you to create a great 3D model.
If you still need more information, make sure to take a look at our tutorial on how to cut costs for your next 3D printing project and which 5 modeling mistakes you need to avoid.
Featured image: Rhino 3D model by Mark Florquin.